Handling of Product quality complaints in pharmaceutical Industry:
Product quality complaints are also known as Market complaints, customer complaints, Technical complaints, quality complaints, etc.
What is complaint: A written or verbal communication received from Consumer, end-user, Client, Caregiver, Pharmacy, Regulatory authority, government agency, Qualified Person, Responsible Pharmacist, Retailer, Distributor, field staff, contract giver, beneficiary, purchaser etc. for the marketed products regarding the Safety, Identity, Strength, Purity, Quality and Efficacy, Labelling, Shortage or any other issue which claims to be related to the quality of the product or packaging shall be considered as market complaint.
Complainant: Any person who receives a commercially distributed product or Regulatory authority or any government agency, Qualified Personnel or Responsible pharmacist, Retailer, Distributor, Field staff, Contract giver, Pharmacy, Consumer, client, end-user, beneficiary and purchaser etc. and who triggers a communication.

Handling of Market complaints:
Handling of market complaint involves the following major stages-
- Logging the complaint
- Acknowledgement & follow-up communication with complainant for additional details (if any)
- Preliminary investigation & assessment for the requirement of FAR
- Investigation
- Root cause and CAPA
- Conclusion of Complaint
- Response to the complainant
- Closure of complaint
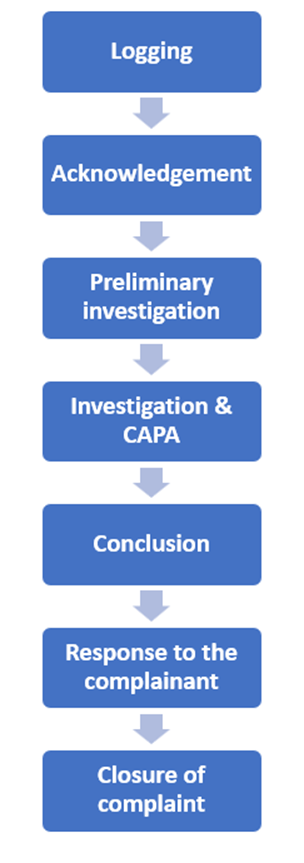
Logging the complaint:
- Quality Assurance (QA) department shall verify the details of complaint such as product name, batch number, pack type, manufacturing site etc.
- QA shall share the information to QA Head and log the compliant in appropriate applications like Track wise, SAP or manually in log book with the available information, within one working day from the date of receipt of the complaint.
- A copy of all the complaint details such as mail copy shall be attach in investigation file.
Acknowledgement of complaint:
- QA shall share the acknowledgment to the complainant within 2 working days from the date of receipt of the complaint.
- During the acknowledgment, any additional information, photographs or samples shall be requested to perform the investigation.
- Copy of acknowledgment shall be attached with the complaint investigation.
- Minimum of three follow-up attempts shall be made to retrieve the details of the batch number and sample if the details are not received at the time of receipt of the complaint.
Preliminary investigation & assessment for the requirement of FAR:
- After acknowledging the complaint, preliminary investigation shall be initiate.
- During the preliminary investigation, complaint shall be categorized in any of the following three categories based on the nature of complaint.
Critical: A complaint where there is significant impact on the quality of the product and patient safety.
Ex: Mix-up, contamination with the foreign matter / material, product not meeting the specification, etc.
Major: A complaint where suitability of use may compromise
Ex: Broken Tablet / capsule, cosmetic defects, abnormal smell / Taste
Minor: A complaint which does not have any impact on quality of the product.
Ex: count variation, damage to secondary packing material
- Preliminary investigation shall be done by reviewing the control / reserve sample, batch manufacturing / packing records, complaint history, etc.
- Each complaint shall be assessed for the requirement of Field alert report (FAR) in case of US market or Quality defect notification in case of other markets to regulatory authority’ within 3 working days from the date of receipt of the complaint. Details of assessment shall be documented in appropriate document. If the decision of filing the FAR, then initial FAR shall be filed within three working days from the receipt of complaint.
Investigation of the complaints:
- QA personnel in coordination with the cross-functional team like manufacturing, packing, QC etc shall initiate an investigation to identify the root cause and complete the investigation within 30 days from the date of receipt of complaint or as per the respective organisation timelines.
- Investigation shall be performed using a structured approach by adopting appropriate investigation tools such as ‘Cause and effect analysis’ (also called as fish bone diagram / 6M evaluation), why-why analysis, FMEA, etc.
- For medical complaints (Adverse events, lack of efficacy), investigation shall be carried out to identify any quality defects. Pharmovigilance team shall further perform the investigation on adverse event or lack of effect complaints.
- QA shall evaluate the complaint or reserve sample. Testing requirement of complaint or reserve sample shall also be evaluated and reviewed by QA.
- Photographs of the reserve sample / complaint sample shall be enclosed in the investigation report wherever applicable.
- For complaints related to count variation i.e. shortage /excess count in a bottle or missing blisters in a carton, the total count of pills in bottle or blister shall be verified and actual count (numbers) shall be documented.
- Investigation shall be done by revieweing of all the below mentioned documents (but not limited) associated records as applicable for any abnormality or incidents.
- Batch manufacturing / Packing record
- Equipment or instrument usage logs
- Personnel training records
- Finished product Analytical reports
- Stability data
- Product quality review report
- Process validation reports
- Relevant QMS data bases like OOS/OOT/Deviations, etc,
- Trend reports, etc.
- Identification and evaluation of repeat complaints: Review the last one year or 2 years (as per organisation procedure) data and check if similar complaints are received.
- If complaint is identified as ‘Repeat complaint’, check whether the CAPA proposed has been implemented and effective.
- Wherever required, perform the process simulation study to evaluate the root cause and CAPA.
- Based on the overall investigation, root cause or probable root causes shall be determined and appropriate CAPA shall be propose.
- Investigation report shall be prepared by the QA including the details (but not limited to) like complaint number, date of receipt, product & strength, batch number, description of the complaint, categorization, investigation team, investigation findings, root cause, impact assessment, interim controls, CAPA effectiveness check plan and list of attachments.
- Investigation report shall be review by QA and revenant cross functional departments. Investigation report shall be finally approved by QA Head / designee.
- Investigation shall be completed within 30 days from the date of receipt of the complaint. If an investigation requires more than 30 days, the complaint co-ordinator shall take an extension on or prior to the due date. To take an extension, an interim investigation report shall be prepared to detail the extent of the investigation carried out and actions taken till date. Site Head / Designee and Quality Head / designee shall evaluate the extension request and provide approval for extension of the timeline.
Conclusion of Complaint:
Based on the investigation findings, categorize the complaint as confirmed / Substantiated or Non-confirmed / Non-Substantiated.
- Confirmed / Substantiated Complaint: A complaint, where the investigation reveals that there is a possibility of occurrence of such defect within the manufacturing process and/or controls of site is termed as confirmed / substantiated complaint.
- Non-confirmed / Non-Substantiated Complaint: A complaint, where the investigation reveals that there is no possibility of occurrence of such defect within the manufacturing process and/or controls of site is termed as non-confirmed / non-substantiated complaint.
Response to the complainant:
A summary of investigation findings (emphasizing the outcomes of the investigation, categorization of the complaint, actions taken, the decision taken on the subject batch, etc.) shall be provided to the complainant.
Closure of complaint:
- For the implementation of corrective and preventive actions, separate CAPA numbers shall be created and track.
- QA shall close the complaint notification after sending the response letter to the complainant.
Handling of complaint samples:
- The remaining complaint samples shall be maintained by QA at the storage conditions specified for the drug product for a period of 5 years or one year after the expiry date of the drug product was received whichever is longer.
- On completion of specified retention period, the samples shall be destroyed and record of it shall be maintained as per the site procedure.
Tracking and trending of complaints:
- QA shall perform the trending of complaints on a quarterly / half yearly basis to understand the trends and take any systemic actions on repeat issues.
- The trending shall include the details but not limited to, number of complaints in each category such as Manufacturing, Analytical, Packaging, Medical, mix-up, Shortages etc. QA Head shall approve the quarterly / half yearly trend report.