BLENDING PROCESS:
Blending of solid particles refers to mixing of solids with the aim of attaining a uniform composition throughout the mix. In powder blending two or more dissimilar particulate solids are blended to give a random mix. Objective of blending is to form a homogeneous final product from two or more dissimilar raw materials.
Blending is the most critical operation in the manufacturing process since perfect homogeneity is practically impossible due to differences in size, shape and density of particles.
MECHANISM OF BLENDING:
Blending inside a blender occurs with the following mechanisms:
- Diffusion or dispersion – the random motion of particles on a small scale (perpendicular to flow)
- Convection – the transfer of groups of particles as a mass (parallel to flow)
- Shear – high forces imparted using baffles to break up agglomerates / cohesion
PROCESS VARIABLES IN BLENDING:
- Proportion of Materials – API versus Excipients
- Blender Characteristics – Octagon versus Cone
- Particle charge – Positive versus Negative
- Particle density – Large versus Small particles
- Blending time
- Blender speed (rpm)
- Temperature
- Humidity
TYPES OF BLENDERS:
Critical to any blending operation is the quality of blend i.e. batch variations. Different applications have varying requirements for product uniformity.
Octagonal Blender:
This blender is used for blending the most delicate and fragile free flow products like powder or granules in 10 to 20 minutes. It is the best way to mix very heavy and abrasive products. The range of products includes colour, plastic, flour, drugs, pharmaceuticals, metal powders, minerals, fibers, and many other.

Double cone blender:
The unique design of the Double cone blender results in a high degree of particle mobility without the use of internal baffles. This type of blender has a low profile, requiring less head-room. The Double cone is a proven performer in a wide variety of industries, offering greater overall volume and high efficiency with blend variations 1 – 2%.
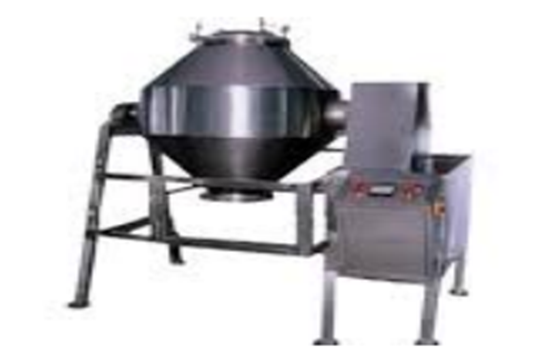
V-Blender:
V – shape blenders are very popular in a wide variety of industries. They offer both short blending times and efficient blending. The blend is achieved by the constant, dividing and intermeshing particle movement provided by two connected cylinders. This precise mixing action results in blend variations of 1 – 2%. Each cylindrical leg has an access cover for easy material loading and cleaning.
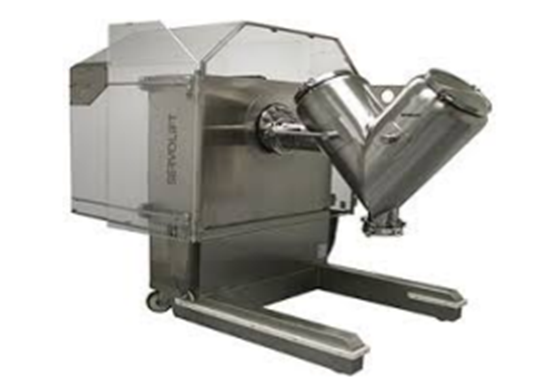
Cone Blender:
The asymmetrical geometry of the slant cone design offers a very fast blend time. High particle mobility, plus the intermeshing action of materials results in blend times up to 33 percent less than other designs. In addition, this concept achieves more control and more precise end product with blend variation as low as 1/2 percent.
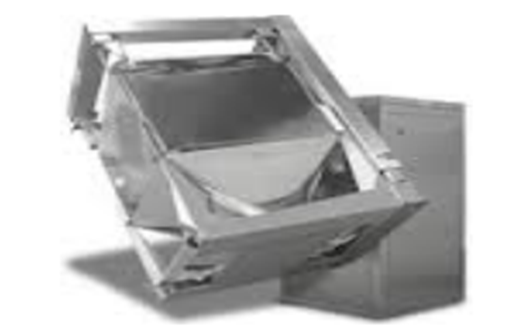
CONSIDERATIONS IN BLENDER SELECTION:
Before selecting any blending system, it is necessary to understand the characteristics of the materials to be blended, how the material is transported to and from the blender, and how the blender will be integrated into the plant.
Key considerations include:
- Material Characteristics
- Loading and unloading requirements
- Easy product changeover
- Man-power availability
- Material lumping
- Single-floor or multi-floor operation
- Daily through-put requirements
- Process flow – Specific industry regulations
- Dust control
- Safety