Granulation is required to improve the flow of powder mixtures and mechanical properties of Tablet.
Granulation is the act or process in which primary powder particles are made to adhere to form larger, multiparticle entities called granules. It is the process of collecting particles together by creating bonds between them. Bonds are formed by compression or by using a binding agent.
Granules typically have a size range between 0.2 to 4.0 mm depending on their subsequent use.
Granulation defined as a size enlargement process which coverts small particles into physically stronger and larger agglomerates having good flow property, better compression characteristics and uniformity.
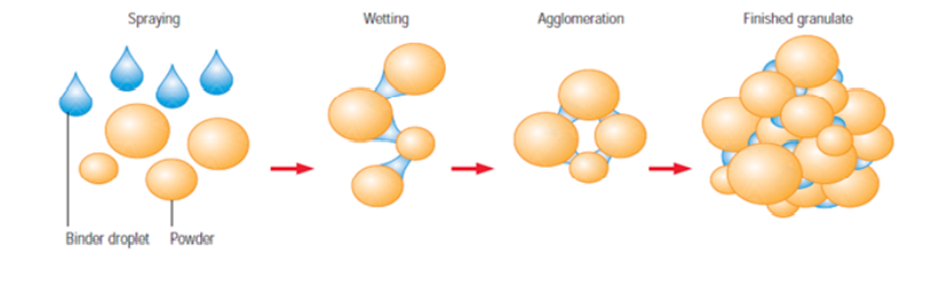
Agglomeration of powders is widely used to improve physical properties like wettability, flow ability, bulk density, and product appearance.
REASONS FOR GRANULATION:
To prevent segregation of the constitutes of the powder mix:
- Segregation or de-mixing is due to differences in the size or density of the components of the mix.
- The smaller and or denser particles concentrating at the base of container.
- The larger and or less senser particles set above the smaller ones.
- An ideal granulation will contain all the constituents of the mixing the correct proportion in each granule and segregation of the ingredients will not occur.
To improve flow properties of the mix:
- Many powders, because of their small size, irregular shape or surface characteristics are cohesive and do not flow well.
- Poor flow will often result in a wide weight variation within the final product owing to variable fill of Tablet dies, etc.
To improve the compaction characteristics of the mix:
- Some powders are difficult to compact even if a readily compactable adhesive is included in the mix and some are compacted easily.
- This is associated with the distribution of the adhesive within the granule and is a function of the method employed to produce granules.
- Solute migration occurring during the post granulation drying stage results in a binder-rich outer layer to the granules.
- This in turn leads to direct binder-binder bonding which assists the consolidation of weakly bonding materials.
Other Reasons:
- Reduce production of toxic dust.
- Reduce possibility of cake formation
- Increase convenient of transport
- To densify the materials
- To facilitate metering or volumetric dispensing
- To improve the appearance of the product.
DESIRABLE PROPERTIES OF GRANULES:
- Controlled size distribution
- Specific granule Voidage – Intragranular Porosity
- Specific bulk density
- Spherical shape
- Adequate moisture
- Good flow
- Good compressibility
- Sufficient Hardness
GRANULATION TECHNIQUES:
- Wet granulation
- Dry granulation
- Direct compression
Choice of method for the manufacture of Tablets is depend on a number of factors like;
- Physical and chemical stability of the therapeutic agent during manufacturing process
- Availability of necessary processing equipment
- Cost of manufacturing process
- The experiences used to formulate the product
WET GRANULATION:
In wet granulation a liquid is required in the manufacturing of granules which are then compressed into Tablets.
Stages of Wet granulation:
Stage 1: Mixing of therapeutic agent with the powdered excipients
Stage 2: Wet granulation of the powder mix
Stage 3: Drying and Sizing (milling) of granules.
Wet granulation techniques:
High shear mixing (Rapid mixer granulator)
Fluid bed granulation (Fluid bed equipment / Fluid bed processor)
Extrusion – Spheronization.
Wet granulation process flow:
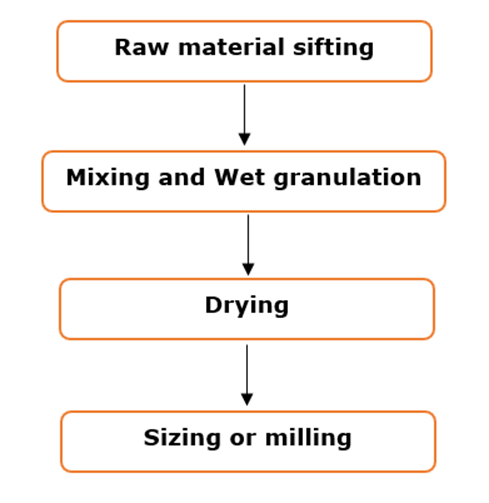
High shear mixing (Rapid mixer granulator – RMG):
RMG is widely used in pharmaceutical industry for granulation. In this type of equipment, the particles are set into movement by an impeller rotating at a high speed. Equipment also contains a chopper, the primary function of chopper is to cut large lumps into smaller fragments thus increases the binder distribution into the blend.
The binder liquid is added by pouring, pumping or spraying from the top. Wet granulation using RMG involves typically 3 phases.
- Dry powder mixing (Therapeutical agent and excipients)
- Liquid binder addition
- Wet massing
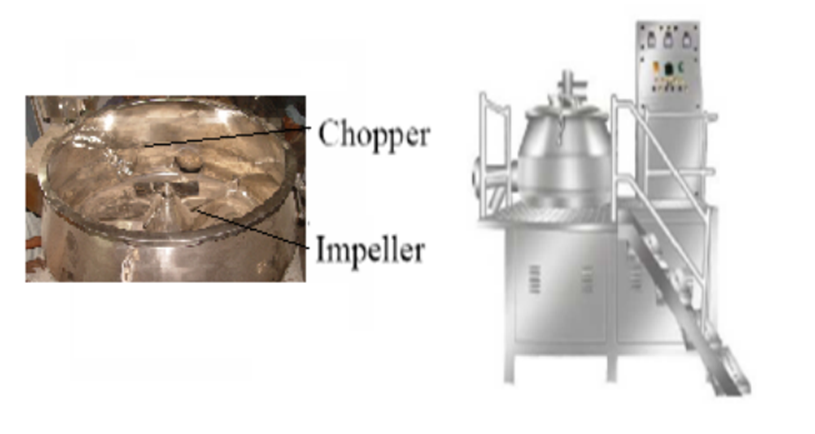
Process: First the materials are dry mixed, where after liquid is added during mixing. Then the moist mass is wet massed in order to achieve a narrow particle size distribution.
Advantages and disadvantages of RMG granulation:
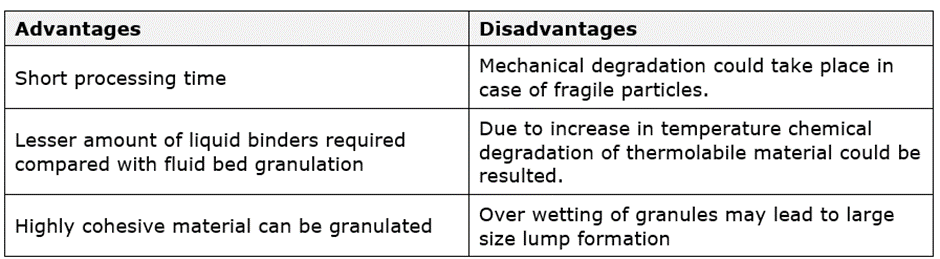
Drying:
Drying is a mass transfer process resulting in the removal of water or moisture from another substance, by evaporation from a solid, semi-solid or liquid to end in a solid state.
Most widely used driers are Fluid bed drier and Tray / shelf drier.
Fluid Bed Drier (FBD):
Fluid bed drying represents a very effective type of solid drying. The whole surface of each individual particle is available for drying in the first phase. Uniform processing conditions are achieved by passing air through a product layer under controlled velocity conditions to create a fluidized sate.
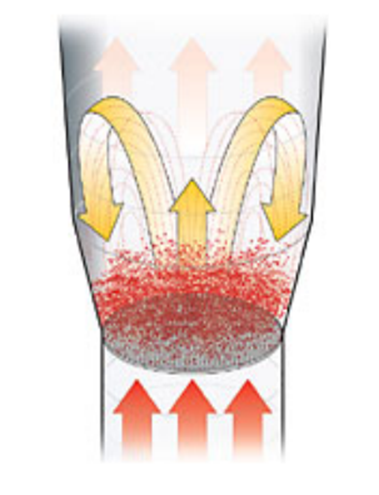
The drying time depends on various factors such as physical properties of material, moisture content, type of moisture, drying temperature, etc.
Sizing or Milling:
Odd-size materials / granules can be reduced to the required size by fitting interchangeable perforated screens around the swing hammer blades. Most commonly used in equipment for sizing are Quadro co-mill and Multi-mill.
Fluid bed granulation (Fluid bed equipment / Fluid bed processor):
Fluid bed granulation is a process by which granules are produced in a single equipment by spraying a binder solution onto a fluidized powder bed. The system involves the heating of air and then directing it through the material to be processed. Later, the same air exit through the voids of the product.
Top-spraying granulation is the most known process for wet granulation. A top spray processor has three components.
- An air handling system which can be equipped with humidification or de-humidification and dew-point control.
- A product container and expansion chamber
- An exhaust system
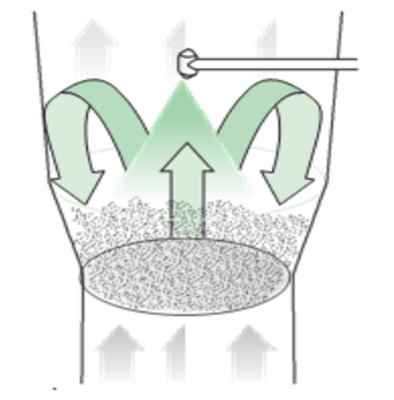
The powders are suspended by a vertical flow of air from the bottom of the granulator. The granulator fluid is sprayed on to the powders from the top of the granulator.
DRY GRANULATION:
The dry granulation process is used to form granules without using a liquid solution in case of moisture and heat sensitive product.
Important steps involved in the dry granulation process are;
- Sifting of raw materials
- Blending of sifted materials
- Compression / compaction into slugs or flakes
- Milling / screening of slugs / flakes
Dry granulation technique:
Either a large Tablet (slug) is produced in a heavy duty tableting press (slugging) or the powder is squeezed between two rollers to produce a sheet of material (roller compacter or chilsonator). These intermediate products are broken using a suitable milling technique to produce a granular material which is usually sieved to separate the desired size fraction. The unused fine material may be re-worked to avoid waste.
Slugging process:
Granulation by slugging is the process of compressing dry powder with Tablet press having die cavity large enough in diameter to fill quickly. Once slugs are produced, they are reduced to appropriate granule size for final compression by screening and milling.
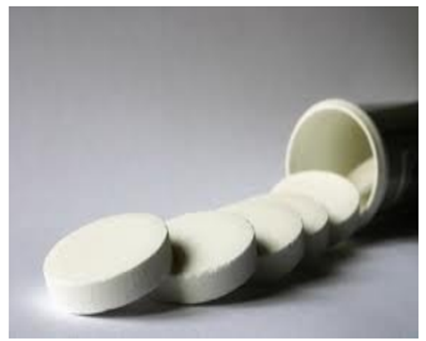
Roller Compaction:
Roller compacter generally consist of three major units;
- A feeding system, which conveys the powder to the compaction area between the rolls
- A compaction unit, where powder is compacted between two counter rotating rolls to a ribbon by applying a force.
- A size reduction unit, for milling the ribbons to the desired particle size.
The roller compacter uses an auger-feed system that will consistently deliver powder uniformly between two pressure rollers.
Roller compaction unit:
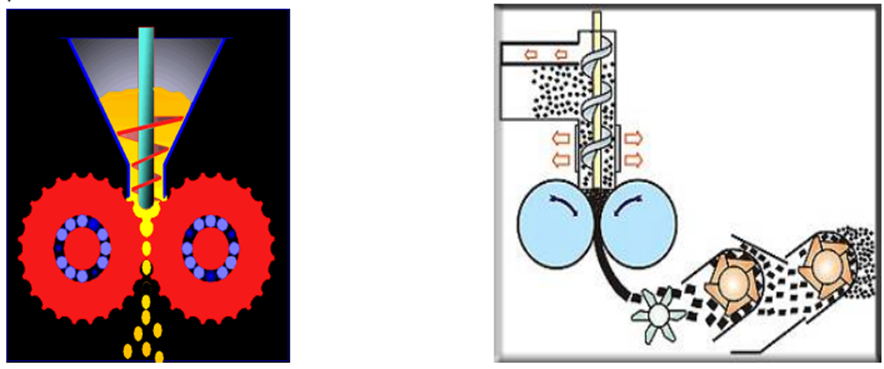
Advantages and disadvantages of dry granulation:
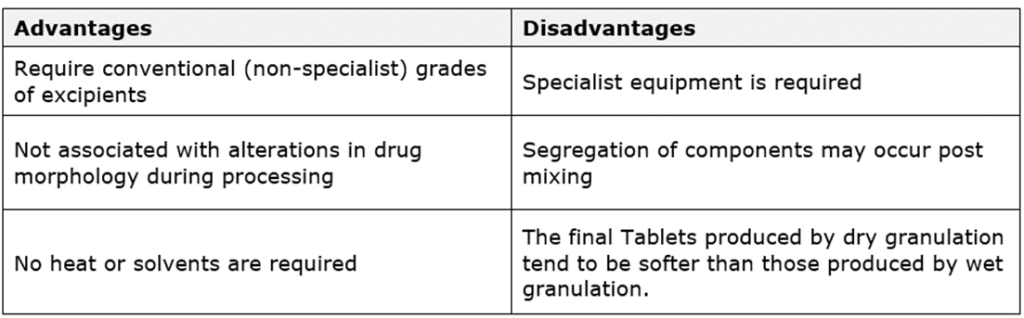
DIRECT COMPRESSION:
Direct compression is the process by which Tablets are compressed directly from powder mixture of active ingredient and suitable excipients. No pre-treatment of the powder blend by wet or dry granulation procedure is required.
Direct compression involves following steps;
- Sifting of drug and excipients
- Mixing of drug and excipients in blender.
Typical unit operations involved in Wet granulation, dry granulation and direct compression:
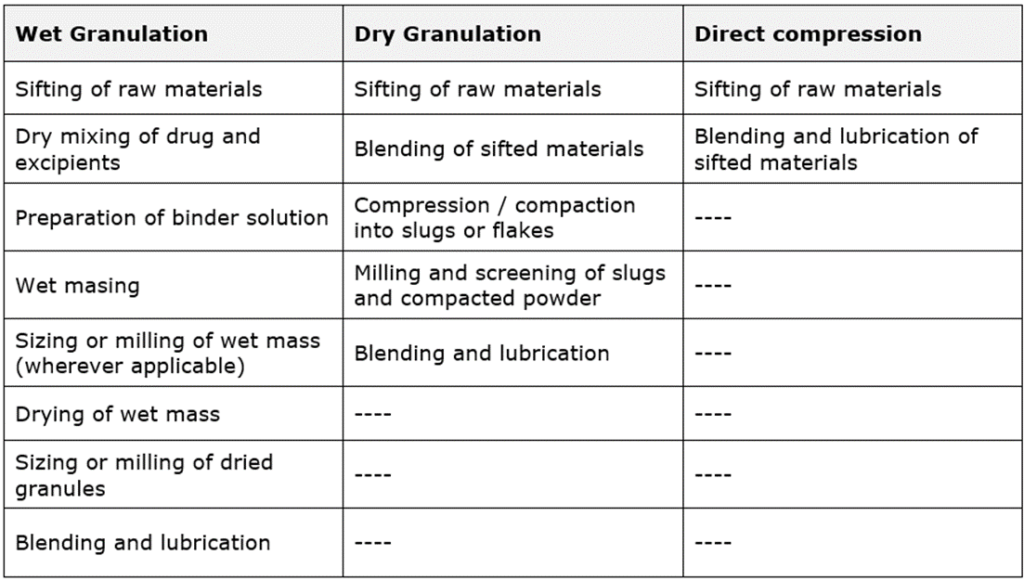